If you are looking for “edgy” art, Bill Herndon, 83, of Acton is your man. He is a custom knife-maker.
Herndon’s passion for creating art in steel began at his father’s side. His father’s hobby was photography and his job was engineering.
Earning a degree in engineering, he then earned a degree one in illustrative design after serving as a photographer in the U.S. military while stationed in Germany in the 1950’s.
After a lifetime in photography and career of selling movie film stock in San Francisco, he retired to Acton in 1997 where he began creating custom knives in his garage.
“When I first started out, I sharpened everything in sight” Herndon said. He sharpened his lawn mower blades and then quickly cut off three toes with it.
Creating his own steel
Herndon wipes the sweat off his face as he stands in front of the 3,000-degree furnace roaring in his back yard.
He is creating a piece of “Damascus” steel, a tedious process perfected in the Third Century in India and the Middle East. The process welds thin layers of steel together and creates distinctive design patterns in a blank of steel that will become a knife blade.
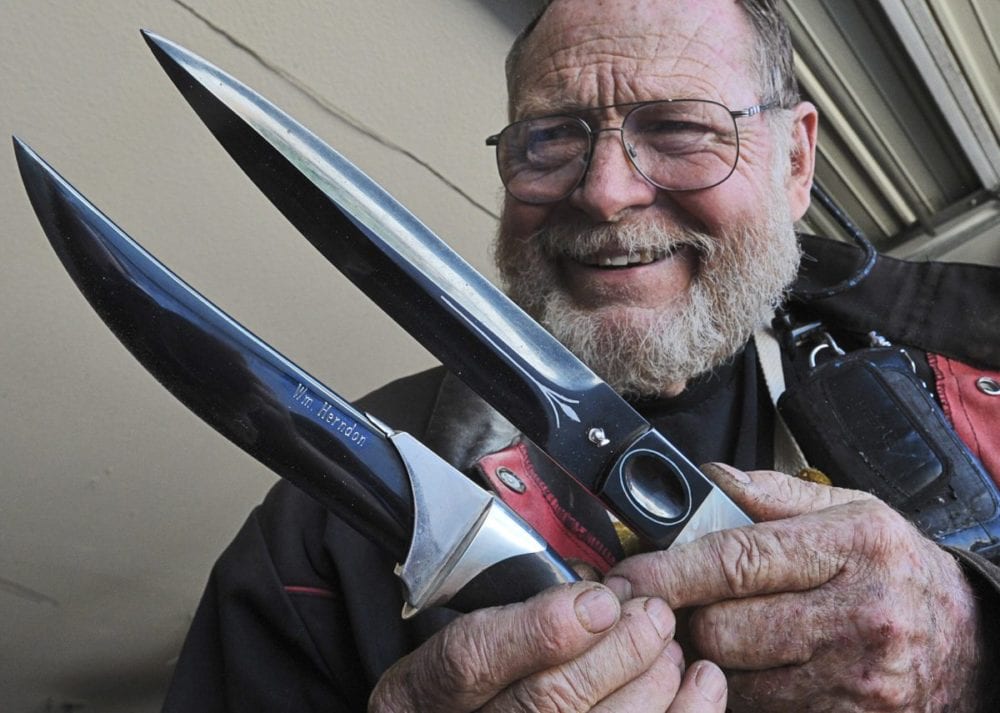
After removing the glowing billet of steel from the white hot mouth of the forge, borax is added to bind the layers. Then 30 tons of force is applied in the nearby press, fusing the strips into one slab of steel.
After repeating the process many times, he moves the blank blade to his power hammer. Activating the six foot tall, clanking, belt driven monster with his foot, Herndon pummels the steel with 50 pounds of pressure at a deafening 250 beats per minute to coax the steel to the thickness of a knife blade.
“Using the power hammer saves my old arms,” he laughs.
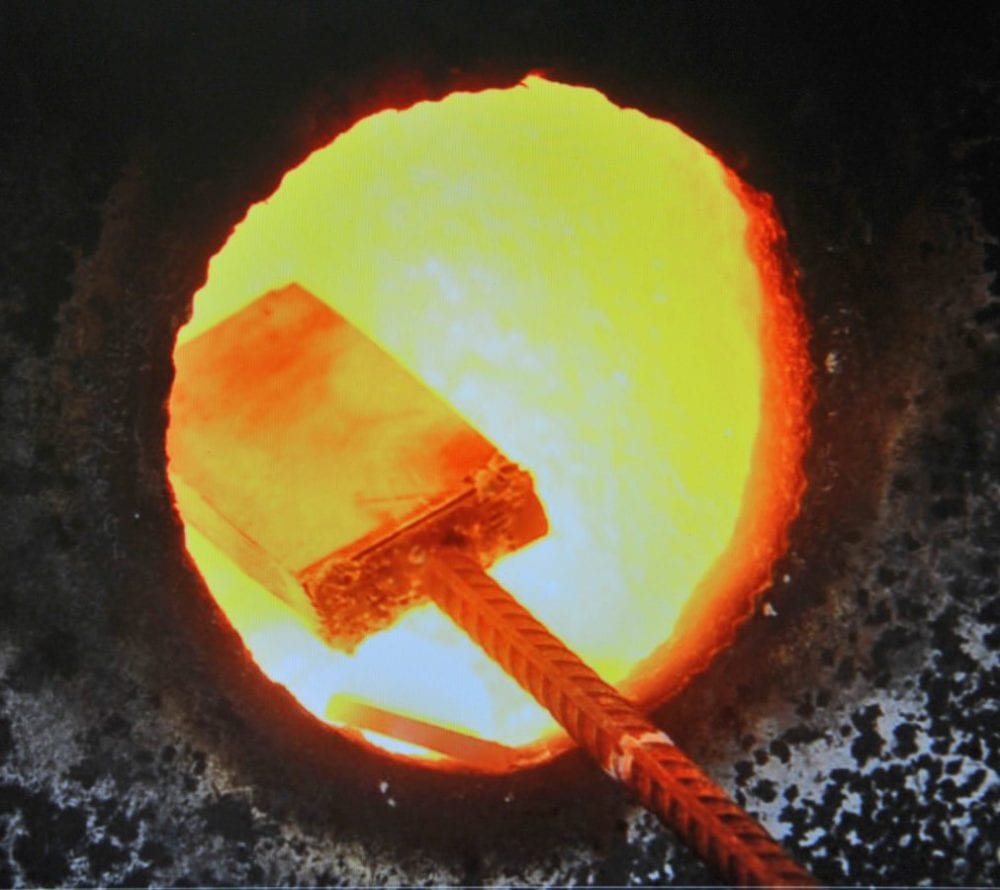
Heating the blade again, he then taps the edge with a blacksmith’s hammer on an anvil to give the blade the familiar curve of a bowie knife.
Work continues in the machine shop
Herndon weaves through the narrow isles between rows of grinders, band saws and drill presses in his garage. His workshop is literally “cutting edge,” with each piece of machinery focused on a specific task in creating his knives.
“Don’t call it a hobby – it’s a vocation,” he said.
Herndon pulls on his scratched glasses, tattered leather gloves and apron. He sits in front of the grinder and touches the steel blade to the whirring belt which throws out a 5-foot shower of hot sparks as he sculpts the steel to rough-out the cutting edge of the blade.
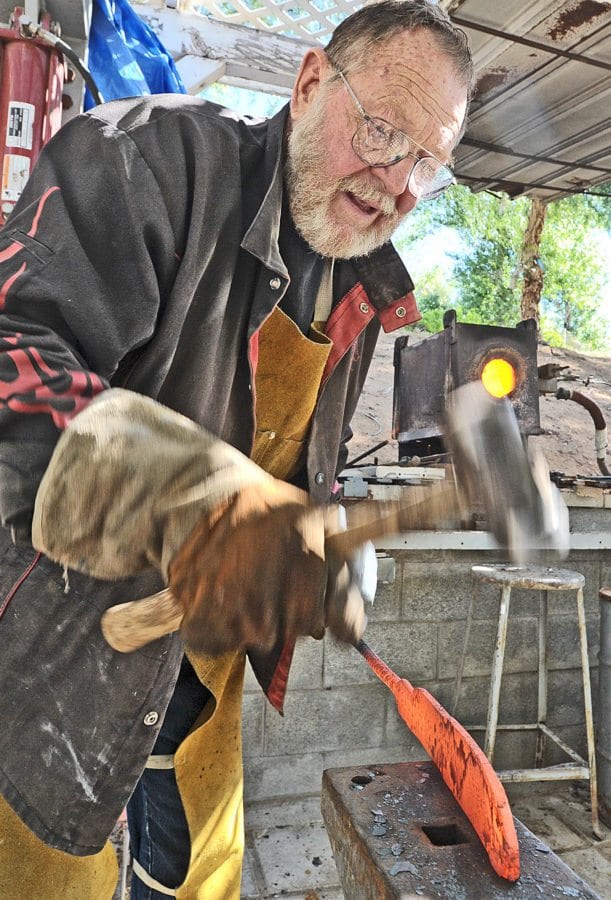
After a series of six grades of grinding belts – from course to very fine – to bring the blade to the proper sharpened edge, it will be sent out for a specific type of hardening determined by its usage for hunting, fishing, fighting, or beauty.
Examining the blade on one of his finished bowie knives, he explains the metallurgy of knife-making and the two distinct tones running the length of the blade.
“This wavy (highly polished) edge is heat-treated to stay sharp; the (dull) back of the blade is left softer and more flexible so it won’t break,” he said.
Running his finger down the craggy, curving handle of the knife, he says, “This handle was carved from Indian stag, which is no longer available in this country.”
This particular knife is valued at $750.00

Herndon opens one of his custom oak display boxes. On the top, the brass label reads Wm. R. “Bill” Herndon. He smiles as he says, “This is one of my favorites.” He lifts the dagger with the smoky dark gray blade and mother of pearl handle from the velvet liner.
“This blade was chemically treated to achieve the dark color,” Bill explains. “This silver inlay is harder to work with than gold. The handle is carved from a $750 piece of mother of pearl.”
He says knife would be worth $2,500.00.
A forged Bowie knife might take Herndon 20 hours to complete, one with a Damascus steel blade will double the hours.
“I make hundreds of knives a year ranging in price from $130 to $5,000 each.” he said. “The price is determined by how much time I have invested in the knife – the more hours – the higher the price. You have to pay yourself something for your work.”
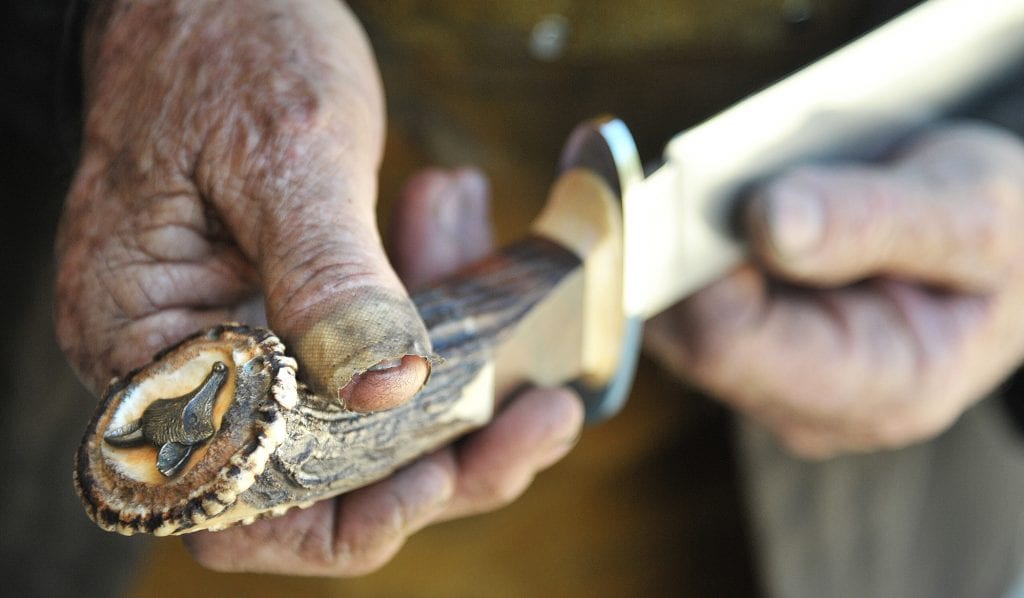