As warehouses aim to manage increasing volumes of goods while controlling costs, vertical storage solutions have emerged as a game-changer. Using a warehouse’s height rather than expanding its footprint, vertical storage maximizes capacity, boosts productivity, and enhances accuracy in picking and inventory management.
Vertical lift modules like the Modula Slim bring innovative solutions to warehouses of all sizes, and this post will explore their key advantages and best practices for their successful implementation.
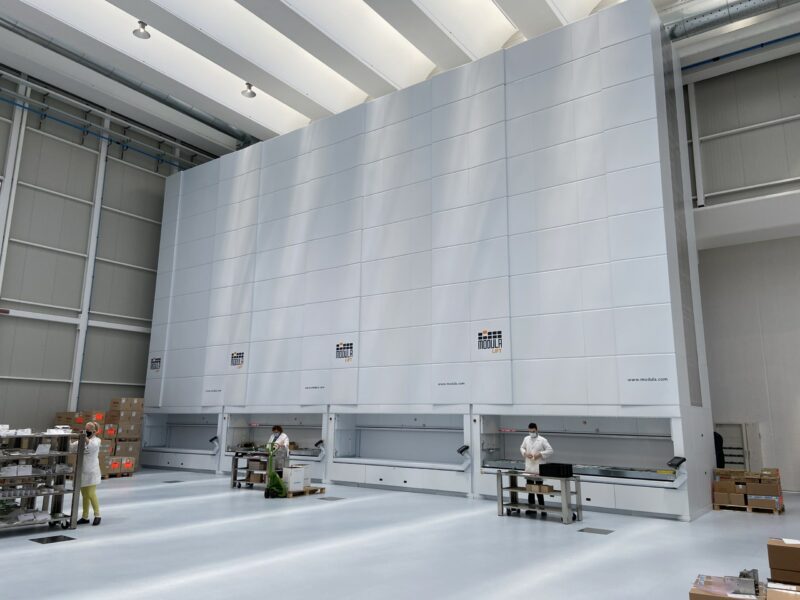
- Maximizing Space
One of the main advantages of vertical storage is the ability to store more in less space. As the name suggests, these systems make use of a warehouse’s often-overlooked verticality. This allows businesses to expand their storage capacity significantly without increasing their physical footprint, a particular benefit in locations where real estate costs are high.
Most vertical storage systems are designed to accommodate a variety of products, from small parts to bulky items. Vertical lift modules, for instance, offer adjustable tray heights and configurations that allow businesses to make the most of each cubic inch.
- Enhancing Picking Accuracy and Productivity
Vertical storage solutions typically feature ergonomic designs, where items are brought directly to the operator at a comfortable height.
This reduces the time workers spend moving around the warehouse to retrieve items, minimizing fatigue and injury risk. The ergonomic setup also speeds up the picking process, allowing operators to fulfill orders more efficiently.
Many systems also include picking aids, such as LED bars and laser pointers, guiding operators to the correct items and reducing picking errors.
- Improving Inventory Control and Organization
Vertical storage systems streamline inventory control by centralizing storage in designated locations and integrating with warehouse management software (WMS). With WMS, every item’s location is tracked digitally, allowing operators to access real-time data on stock levels, location, and order status.
This automated tracking improves inventory visibility and reduces the risk of stockouts or overstocking, creating a more efficient and balanced inventory flow.
- Flexibility for Diverse Warehousing Needs
Vertical storage is highly adaptable. These systems can store a variety of items, from small, loose materials to larger components, making them versatile across industries.
With adjustable tray heights, modular configurations, and custom accessory options, warehouses can tailor vertical storage to their specific requirements. As inventory changes over time, these systems can be reconfigured, making them a flexible, long-term warehousing solution.
- Energy Efficiency and Sustainability
As businesses prioritize sustainability, energy-efficient solutions become increasingly valuable. Many vertical storage systems consume relatively little energy compared to traditional storage methods, thanks to modern power-saving technologies.
For instance, advanced VLMs often come with efficient motors and energy-saving modes, lowering electricity usage and reducing operating costs over time.
- Simplifying Installation and User Training
Compared to large racking systems, vertical storage units are simple to install and require minimal downtime. Many systems are modular, allowing quick setup and easy reconfiguration. Additionally, vertical storage systems often feature intuitive touchscreen interfaces and simple controls, reducing the amount of training needed for operators.
Educating staff to use these systems efficiently ensures a smooth workflow and reduces the likelihood of operational errors. Quick onboarding means warehouses can adopt vertical storage without significantly disrupting their day-to-day operations.
Best Practices for Implementing Vertical Storage Solutions
To make the most of vertical storage, it’s important to consider these best practices:
- Conduct a storage-needs assessment: Before selecting a vertical storage solution, analyze your inventory needs and the types and quantities of items you handle. This will help determine the correct configuration, tray sizes, and features.
- Invest in staff training: Properly training staff on how to use the storage system, especially any automated features, is essential for maximizing its benefits. Ensure operators understand the best ways to organize items, access stored products, and use the system’s digital controls.
- Integrate with warehouse management software: Connecting vertical storage to a WMS enables real-time inventory tracking, optimizes order picking, and reduces manual errors. If your warehouse doesn’t already use a WMS, consider implementing one alongside your vertical storage solution.
- Organize items for quick retrieval: Place high-frequency items in easily accessible trays while storing less commonly used items higher up. Organizing items in this way can speed up order fulfillment and minimize operator movement.
- Schedule regular maintenance: While vertical storage systems are generally low-maintenance, regular inspections and upkeep can extend their lifespan. Be proactive about checking mechanics, software updates, and controls to avoid disruptions and keep the system running smoothly.
Conclusion
Vertical storage solutions are transforming the warehouse industry, providing an effective way to optimize space, improve productivity, and enhance inventory accuracy.
These systems offer a versatile, sustainable solution for warehouses looking to increase efficiency without the need for additional square footage — a smart choice for businesses aiming to scale efficiently and sustainably.