By Mike Letson
Signal Contributor
“A place for everything and everything in its place” is a maxim that’s familiar to most of us.
What you might not know is that more than just an old saying, it’s also another way of expressing the Lean Principle of “5S,” a proven methodology for creating and maintaining an efficient and effective work space.
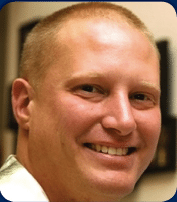
These steps originated in Japan as part of the journey towards a visual workplace, where problems — i.e., out-of-standard conditions — are immediately obvious, thus more readily fixable.
The steps:
• Sort – Get rid of what you don’t need and keep what you do
• Set in Order – Once you know what you have, organize it
• Shine – Clean and inspect your tools so they work when you need them
• Standardize – Evaluate and improve, and stay consistent where it makes sense to
• Sustain – Keep it up because it works
Over the years, as we’ve evolved and the world of continuous improvement has changed, we’ve added two more elements to the mix, safety and security.
The obvious question is, “Shouldn’t safety be considered in all five aspects of 5S?” Yes, but with a greater emphasis. For the last three years, lost time at work due to recordable injuries has been steady according to the State of California Department of Industrial Relations.
That’s not progress. This is an opportunity to enhance an existing program and help to improve what we all know is our greatest resource – people.
Security, the 7th S, has two main categories: physical and intellectual. Physical security includes things like access to buildings, areas of buildings and specific rooms.
Examples of questions that need to be answered include, “Who has the keys to this lock?” and “What times should people be in certain areas of the building?”
Taking security and preparation seriously should include an emergency preparation plan and mandatory recurring training for all employees.
Intellectual security deals with intellectual property and information. This can include anti-virus software and firewalls, controlled access to files and documents based on need, and restrictions of professional conversations.
Behavior and culture are critical factors to consider when evaluating your business. Many safeguards can be put in place to prevent and deter security breaches. An easy step to take is to increase awareness of existing and potential issues.
When implementing a 7S Program at your workplace, either from scratch or modifying/updating an existing one, consider the following:
• Plan the program, don’t just jump into it. This is not a “hurry and get it done” program.
• Audit sheets should include all 7 S’s. This will increase the focus on the needed areas.
• Stay aware of potential issues and hazards, and fix them once identified.
• Write or update your emergency preparation plan and train with it regularly. It will pay off!
• Make training fun and memorable, and don’t treat it like another additional requirement.
We can all be better organized and work more efficiently. Consider the 7S Program as an opportunity for continuous improvement.
Mike Letson is a Business Advisor with the Small Business Development Center (SBDC) hosted by College of the Canyons, as well as a Certified Scrum Product Owner and Certified Lean Six Sigma Black Belt. Mr. Letson’s column reflects his own views and not necessarily those of the Signal. For more information about how the SBDC can help your business, please call 661-362-5900, or visit www.cocsbdc.org.