Not many adults, let alone fourth graders, assemble 3D printers at home, but that’s exactly what Nathan Shyam did — not once, but twice.
Shyam, 13, who’s now an eighth grader at La Mesa Junior High School, spent years perfecting the first prototype, along with the assistance of his dad, Shyam Raghavan.
“My fourth-grade teacher got a 3D printer, and I really liked it. I used to build Legos, so I thought, ‘Oh, if I had it, I could make my own Legos.’ But turns out that’s illegal,” Shyam said. “Ever since then, I wanted to make one and then the idea really came to me the summer after fourth grade. We spent a year building it, but it didn’t work out. But after doing a test print, we saw what went wrong and how we could improve. Finally, it was perfect.”
Despite the first model being nearly perfect, Shyam realized a problem with his printer two years later — when he was a sixth grader.
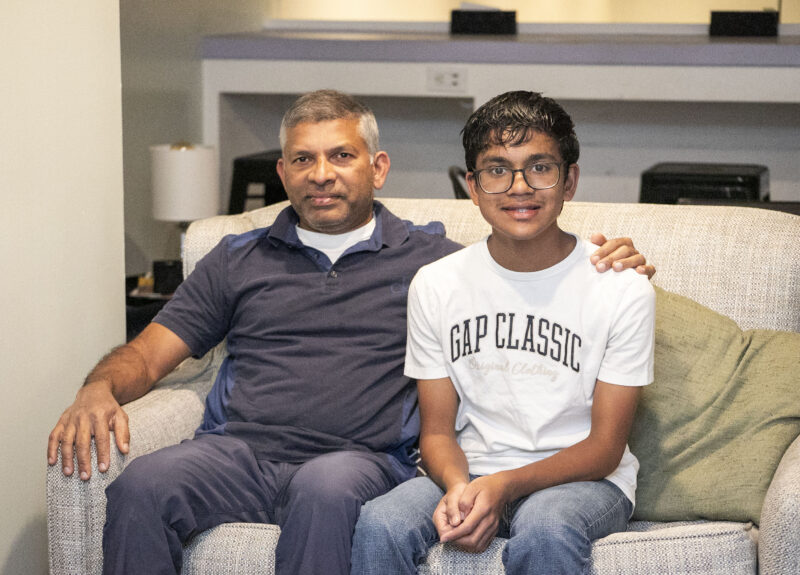
“I started to make an RC car, but then when I was printing it the gears were printing at an angle. So that’s why I made the new one,” Shyam said. “The first one was actually held up by hot glue. It was shaking, all hot.”
Starting in December 2022, Shyam finished his new printer on Sunday. The process to build another printer for Shyam is now second nature and seamless given his newfound expertise.
“There are three axes — x, y and z. So first, you build the y-axis, because that’s the base. So to make that, it needs to slide around. You need two linear rods, like a metal rod that’s really smooth and bearings, otherwise there will be vibrations,” Shyam said.
To make the printer move back and forth, one would need a lead screw. In addition to a stepper motor, which can be coded, the printer will need coupling.
“Coupling attaches the lead screw, the thing that actually makes it move back and forth, and the motor together,” Shyam said.
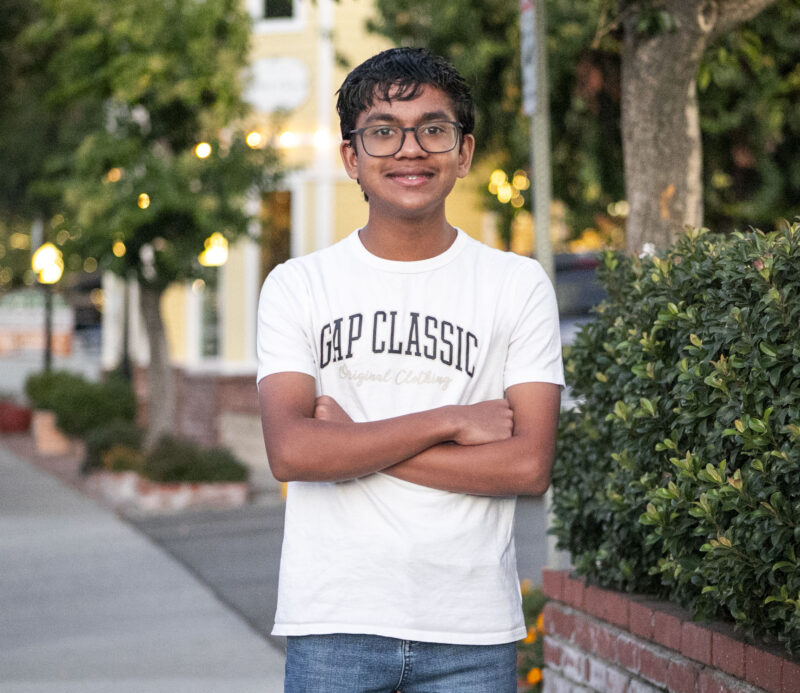
“From then on, you build the z-axis— that’s what makes the nozzle, the printhead that melts the film and places it down, move up and down. You make that with bearings, rods, motors, the same things,” Shyam said. “The x-axis is just a smaller y-axis and you put that on the z-axis, and then you assemble the frame together and code it. There are open-source software that you can download and just put in your parameters.”
Shyam not only has his blueprint down, but also boasted about how fast his 3D model is compared to the current market.
“A lot of the printers on the market, not all but the ones that people usually buy, are all belt drives to make it more cost-efficient. The problem, though, is since it’s driven by a belt, the belt has some slack in it, so it’s not very accurate,” Shyam said. “You can dial it in but it’s not that great. Mine doesn’t use a belt, it uses a solid metal lead screw so that it will move around.”
Shyam now uses Autodesk Fusion 360, a computer-aided design software, to design his prints, but used to use Tinkercad, which is what he was taught in the fourth grade. Initially, Shyam did not have much of an idea of how to go about his first project, but with the replacement of three motherboards, and many improvisations later, he learned.
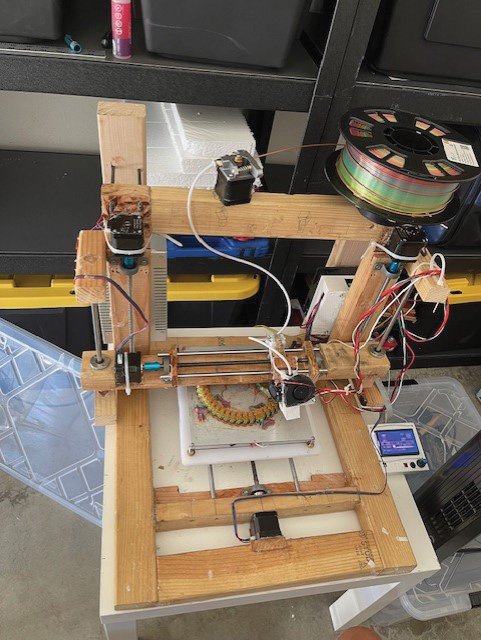
“In the beginning, I didn’t have much of an idea, so I bought random parts I saw,” Shyam said. “I watched a lot of these videos on YouTube and saw people making awesome things. This guy, for example, made the world’s fastest jet RC car.”
Feeling inspired, Shyam was dedicated to creating his car. Finding that it was hard to print an RC car with the first printer, he has yet to print one to his satisfaction. However, given that Shyam is printing with polylactic acid, which is prone to melting, he is hopeful he can discover the proper technique, or even begin using other materials with his new printing model.
“I use PLA, [but there’s] ABS, nylon, TPU, carbon fiber. Now there’s this new technology where you can print with metal. I’m trying to get into that too because I really want to make metal parts, which may even solve the entire car problem.”
Raghavan elaborated on Shyam’s dedication to creating his dream printed car.
“He wanted to create a second version of his printer because the gears were rubbing against each other, and he wanted to send the car to 100 mph. When it goes and spins really fast, the vibrating heats up the plastic,” Raghavan said.
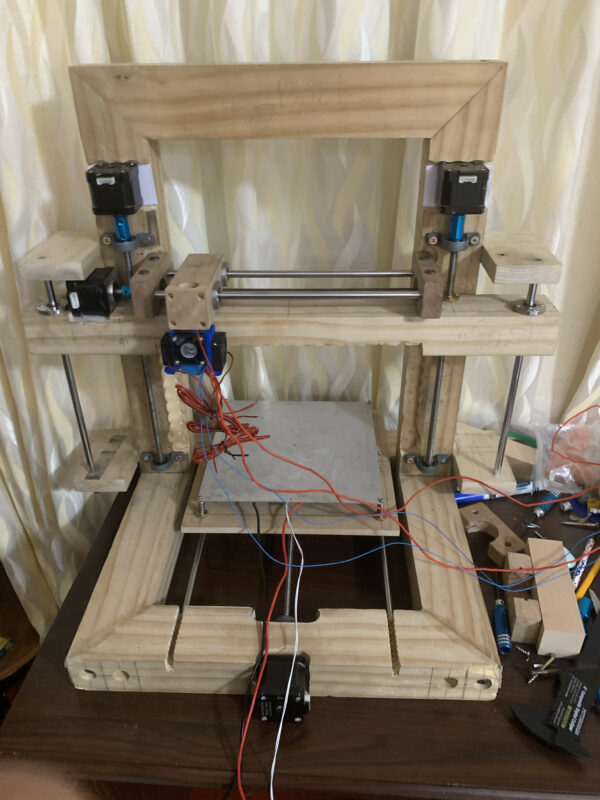
The two printers have allowed Raghavan and Shyam to bond and learn about the process together, implementing Raghavan’s skills as a software engineer and Shyam’s curiosity as a future mechanical engineer.
“I’m really proud of him because he didn’t want to compromise the accuracy of the printer when rebuilding it,” Raghavan said. “I think the most challenging part of the second version was the y-axis, because the bearings were not aligning. We had to go to this metal store to cut the wood accurately for the second printer, and we were going back and forth.”
Now that the second printer is done, Raghavan raved about his son’s ability to understand the process, as well as stating that it is now a tool for the physical realization of Shyam’s imagination.
“His real goal is to build things, and he’s only 13 and an expert in a design studio,” Raghavan said. “It’s a great platform for him to print his ideas — the printer is a base.”
As for Shyam, his advice for anyone who is courageous enough to build a 3D printer is to be meticulous.
“Never compromise, always try to make everything perfect,” Shyma said. “Whereas if you don’t, on such a machine, it might not end well. Because then problems arise from everywhere, 1,000 problems.”