It is well known that the medical industry has high requirements for equipment out of its particularity. Nowadays, high-quality CNC(Computer Numerical Control) aluminum parts are widely applied in the healthcare industry. From surgical instruments, and dental devices to imaging and implanted equipment, aluminum CNC parts are becoming increasingly popular due to their excellent and stable performances.Â
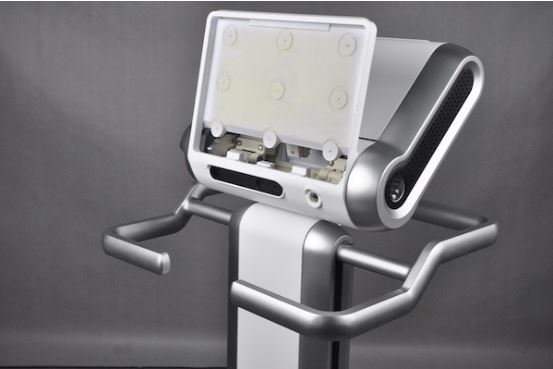
On the one hand, it is lightweight and highly strong simultaneously. On the other hand, it’s precise and biocompatible. This article mainly focuses on the different applications of aluminum parts in the medical industry.
Light Weight and Corrosion Resistance for Surgical Instruments
Aluminum alloy is the first choice for creating surgical instruments due to its lightweight and corrosion resistance. Above all, the material strength is an important factor for manufacturing surgical instruments including scissors, clamps, hooks, scalpels, etc. Aluminum is a suitable material for CNC machining because of its lightweight and high strength.
Aluminum is uniquely light which is one-third the weight of steel on average. At the same time, its density is lower and not strong as steel. So, aluminum is developed as aluminum alloys which are in common use for manufacturing. If only considering the strength of each material by weight, the performance of aluminum alloys even exceeds that of steel. CNC aluminum parts are preferred when engineers are figuring out how to reduce weight but maintain strength.
What’s more, surgical equipment is often in contact with biological fluids and other media for long periods, contaminated with a variety of bacteria and pathogens. Due to the aseptic requirements of medical operations, the devices will be disinfected several times before use. Therefore, high demands are placed on the corrosion resistance of the material.
Normal metal materials are apt to rust. Aluminum is resistant to sterilization procedures, and they’re virtually rust-free after surface finish, which effectively assures the material’s durability. As non-toxic and non-reactive materials, they lower the risk of infections and complications exactly during medical procedures. With the advantages of lightweight, high-strength, and corrosion-resistant, 6061 aluminum alloy is highly recommended.
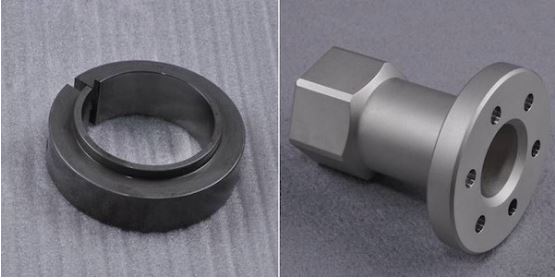
Efficient Heat Dissipation In Medical Imaging Devices
From X-ray machines, magnetic resonance imaging (MRI) machines, and computed tomography (CT) scanners to ultrasonic instruments, medical imaging devices are essential for accurate diagnoses and treatment planning. When the imaging devices are in operation, a great amount of heat is generated from high-performance electronics components. You are probably well aware that it’s extremely important to keep those highly sensitive medical gear at the proper running temperature.
Aluminum heatsinks offer outstanding thermal conductivity and efficient heat transfer. Thermal conductivity measures a metal’s ability to heat conduction. It means that the aluminum cools the temperatures in the act of heat dissipation. The heat inside the critical components is rapidly transferred to outer heatsinks, liquid cooling lines or even to the enclosures. So, the heatsinks installed can dissipate a great deal of heat, to prevent excessive temperature rise in critical components and keep stable operating temperatures.
Heat dissipation of Aluminum parts ensures the performance and operation safety of imaging devices. The aluminum heatsinks not only maintain optimal performance and prevent damage to sensitive components but also extend the life span of imaging devices.
What’s more, the aluminum CNC parts are used to create imaging devices including their housings, brackets, bases, or partitions. Due to great thermal conductivity, they effectively assure precise and safe surgical procedures.
Dental Devices Made of High precision Aluminum
Aluminum alloy is a commonly used type of material for producing various dental devices such as drillers, sickle probes, ultrasonic tooth cleaners, and so on. Each delicate maneuver within the oral cavity require dental tools of tight tolerances as well as specific shapes. And CNC 5-axis machining can create precise aluminum parts for dental devices. The advanced and flexible machining capability of 5-axis machines is helpful to customizing delicate dental tools, particularly for complex dental surgeries or procedures involving patients with unusual oral structures.
Aluminum is prominent for its excellent machinability. Despite complex structures, 5-axis CNC machines can efficiently machine several dental tools such as retractors with smooth and clean surfaces. High precision and reliable quality contribute to exceptional and excellent performance. Furthermore, Various types of surface finishes, such as bead blasting, Anodic oxidation, and polishing can be applied to dental tools. For example, bead blasting is used on teeth cleaning whitening tools and dental saliva suction valves for visual and functional needs. Â
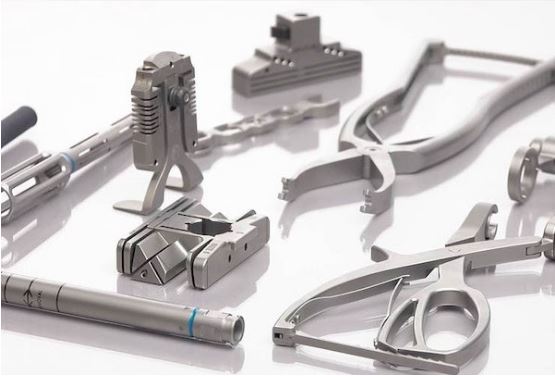
With sophisticated aluminum dental devices, experienced dentists can reach anywhere in the mouth easily and offer patients first-class dental care. Apart from dental devices, aluminum CNC parts are used in the manufacturing of stretchers, hospital beds, crutches, armrests, prosthetics, and rocking chairs. In addition, the price of aluminum is relatively less expensive, especially for standard parts and higher volume. As a result, using aluminum alloy is a cost-effective and affordable solution for manufacturing medical instruments without compromising performance.
Biocompatibility For Implanted Devices
The biocompatibility of materials means that it isn’t harmful or toxic to living tissue. This property is very essential for the manufacturing of implanted medical devices, such as dental implants and temporary bone fixation plates. As a biocompatible material, aluminum CNC parts can be implanted into the human body or make direct contact with tissues without causing harm, providing better biocompatibility than many other materials. Its unique property mitigates the risk of infections during medical procedures or any long-term problems. In this way, it indeed ensures patient safety and speeds up wound healing.
Besides, most implanted devices are precisely tailored to the patient’s demands. Even the slightest deviation in size can lead to patient discomfort, potentially leading to unwanted local, tumorigenic or systemic effects. Then it is necessary to point out a way to achieve high accuracy on implanted devices. Because of powerful precision machining capabilities, 5-axis CNC machining is an ideal manufacturing process for machining complicate aluminum implanted parts.
ConclusionÂ
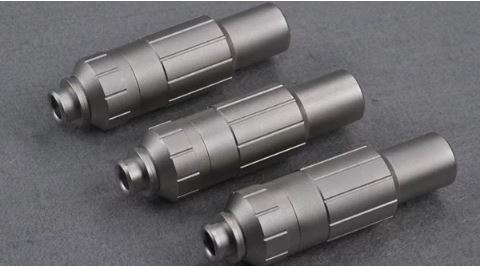
As mentioned above, there are numerous applications for aluminum parts in the medical industry because of their lightweight, high precision, biocompatibility, and effective cost. They can not only support accurate diagnoses, and improve the efficiency of the operations but also offer convenient and simplified healthcare services. With the development of advanced CNC machining technology, aluminum CNC parts will play a key role in shaping the future of the medical industry.Â